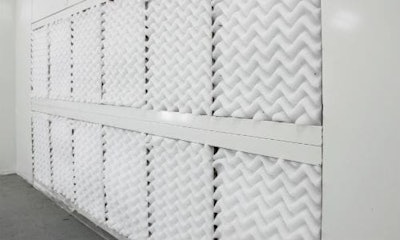
Osseo, Wisconsin — February 14, 2017 — Choosing the correct filter for your paint booth can be a daunting task. The choices you make will have a direct impact on everything from the efficiency of your booth and the quality of the end product to booth maintenance costs and the safety of technicians. This article will introduce you to and give insight into the different types of filters found throughout your booth, as well as maintenance tips to keep your booth running efficiently.
Air make-up
Depending on your booth setup, your first line of filtration defense might be air make-up filters. Located in the air make-up, these filters trap large particles before air reaches the air make-up unit, which provides pressurized air to the spray booth. As well as providing filtration for the air make-up unit itself, the filters play an important role in extending the life of more expensive filtration further down the line. Air make-up filters come in multiple varieties such as pad filters, panel filters, cleanable aluminum filters, and pocket and bag filters.
When troubleshooting airflow issues, the air make-up filters are a good place to start. If you have insufficient airflow, the filters may be dirty or clogged, and if you are getting too much airflow, check to ensure the filters are correctly in place. In addition, keep in mind that with air make-up filters in many units, a burner or cooling coil is located directly behind the filter frame system, so care must be taken that filters do not come in contact with the burner or coil.
Intake
It only takes particulates around 10 microns to cause a defect on your paint job. For reference, that’s about 0.0004 inches! This highlights the importance of intake filters. They provide clean, filtered air to the booth, so your coating operation is free of foreign particles that can contaminate your paint job.
The type of booth also affects the type of filter required. For crossdraft booths, the filters are often internally supported polyester panel filters or linked panel filters, which are typically designed to be installed without the aid of clips or other mounting hardware while creating a leak-free static fit when inserted into the frame. A common type of filter used in downdraft booths is a diffusion type media pad. This type of filter allows the airflow to spread uniformly throughout the booth, ensuring optimal conditions for applying coating.
Because each type of booth uses different filters, the efficiency of the filters also differs. The polyester panel filters or linked panel filters for a crossdraft booth will vary from a minimum efficiency reporting value (MERV) 6 to 8, with GFS providing MERV 7 products with its crossdraft booths. The diffusion type media pad found in a downdraft booth is much more efficient, with a MERV 10 or higher. This rating ensures an internal cleanroom atmosphere that removes more than 99 percent of all particulates 10 microns or larger from the air entering the booth.
Exhaust
Where intake filters ensure that you are working with clean air from the start, exhaust filters make sure the air leaving the booth will be safe for the environment, while also keeping potentially dangerous chemicals from remaining in the airflow of the booth. Exhaust filters capture solid and liquid aerosols that painters can be exposed to through inhalation or dermal adsorption. The filters also keep those highly toxic materials from being released into the environment after passing through the booth.
Another main goal of exhaust filtration is to protect your fans, stack and plenum from the buildup of overspray contamination. In order to do this, exhaust filters need to be able to hold enough paint to avoid constantly replacing the filters, while at the same time providing a minimal pressure drop within the booth to ensure particulates don’t harden and end up on the painted surface.
Most paint booths typically use single-stage filters. The type of exhaust filter used is the same for crossdraft and downdraft booths but the location and frame configuration differ. In crossdraft booths you will find plenum or wall filters, whereas in downdraft booths, exhaust pit filters are used.
The filters themselves are generally made of multilayered polyester and/or fiberglass. Differences in fibre configuration, density and composition all impact how any exhaust filter will perform.
Filter maintenance
Just as important as deciding which filters to use is establishing a regular schedule for changing the intake and exhaust filters. The cleanliness of your spray booth and the work you do within depend heavily on it. Clogged or overloaded filters may not allow proper airflow through the booth, causing dust or overspray to recirculate through the booth and affect the finish of your paint job.
Beyond that, it is also an important step in ensuring your paint operation meets the health and safety standards required by OSHA and NFPA regulations. In more severe situations, clogged filters may create flammable or explosive conditions within your booth.
The problem is that with so many different styles and brands, filters will reach their “target” reading and require replacement at varying rates. These rates also depend upon the paint type, booth design, fan speed, temperature, spray equipment, etc.
One way to establish a change-out schedule for exhaust filters is to compare readings from a manometer or magnehelic pressure gauge with the booth manufacturer’s specs. Without a pressure gauge, it is best to establish a strict maintenance schedule based on the volume of spraying taking place on a day-to-day basis.
Ultimately, it is best to work with your spray booth manufacturer or filter supplier to design an effective schedule for changing your filters that finds a good balance between filtration needs and cost efficiency in your booth’s performance.
The information in this article comes courtesy of GFS. For more information on GFS products and solutions, please contact Mick Ramis via email to MRamis@globalfinishing.com.