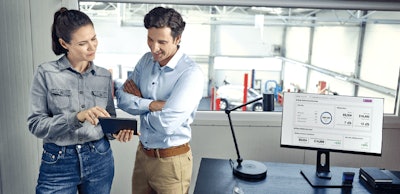
3M™ RepairStack™ Performance Solutions automates material tracking, invoicing to enhance profitability
Story by ALLISON ROGERS
There are three major components of consideration when it comes to 3M™ RepairStack™ Performance Solutions benefits, according to Ryan Fuller, digital solutions marketing manager for 3M™.
“3M™ RepairStack™ was put together based on requests we received specifically from bodyshops. It all comes back to improving how you operate your business. We want to help collision centres run a better business, not just a better bodyshop,” Fuller told Collision Repair.
3M™RepairStack™ is more than an innovative storage cabinet. The technology tracks material usage and re-orders product when needed, which keeps your skilled repair personnel away from irrelevant tasks and on the specialized jobs where they’re really needed. The billables invoicing component allows collision centres to accurately document repairs and report materials to get paid appropriately for all the components used in that job. Data from materials, invoicing and sales can be compared for advanced visibility on gross profitability, efficiency, sales per estimator, sales per technician, use of material compared to labour hours and much more.
Fuller pointed out that, in 3M’s conversations with collision centres, the number-one problem is labour. “It’s two different angles of the same problem: either they can’t get people at all, or there’s some people, but they don’t have exactly the right skills. 3M™ helps that problem by automating operations that can be automated; whether it’s integrations with bodyshop management systems, distributor management systems, integrations with paint portals, et cetera.
“By automating these operations, the skilled labourer can focus on the skilled projects they need to,” Fuller explained. Precise material usage reports can provide far more information than you may think. Materials are categorized when staff remove them from inventory; the exact volume and dollar amount of that material will be recorded on the repair order and in your files.
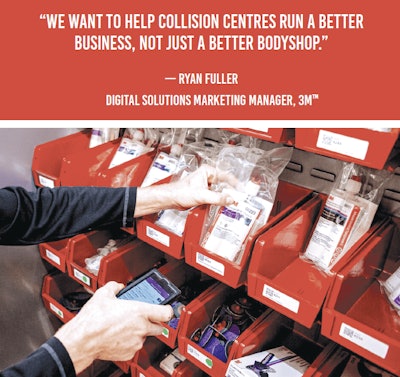
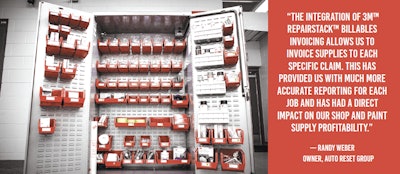
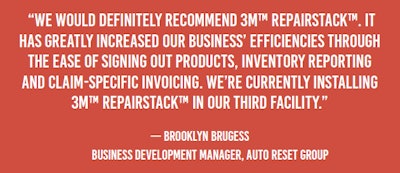
“Say technician A goes through about $3 of abrasive per job, and you see via 3M™ RepairStack™ that an apprentice is using $6 of abrasives per job. We can look into it, figure out why that apprentice may be using more than they need, address the issue and ultimately use fewer materials, and save money,” explained Fuller.
“You can also compare dollar amounts per job; dollar amounts per labour hour and other data to track against yourself and compare over time.” 3M™RepairStack™ can be integrated with two different bodyshop management programs available to the Canadian market: BodyShop Connect and Axalta ProfitNet.
Solutions are customizable to the collision centre’s liking. If you seek the 3M™ RepairStack™program with built-in billable invoicing only, there’s an option for you. Perhaps you have an organized space for your materials already and you don’t need the full 3M™ RepairStack™ cabinet, just the scanner. Or you can opt for the full suite of solutions—cabinets, software, scanner and all—to achieve your desired results.
Randy Weber and Brooklyn Brugess from Auto Reset Group in Ontario have been using 3M™ RepairStack™ at their CSN Walkerton location for more than year now. They first received the recommendation from Brown’s Auto Supply.
“The main selling feature for us was the ease of signing out products for our technicians, as well as the integration of 3M™ RepairStack™ Billables Invoicing,” Brooklyn, business deveopment manager for Auto Reset Group, told Collision Repair.
“Introducing 3M™ RepairStack™ at two out of our three total facilities has been a very positive change, not only for our technicians signing the products out on the floor, but also for our administration team,” added Randy, owner and president of Auto Reset Group. “The integration of 3M™ RepairStack™ Billables Invoicing allows us to invoice supplies to each specific claim. This has provided us with much more accurate reporting for each job and has had a direct impact on our shop and paint supply profitability.”
“We’re setting 3M™RepairStack™ up at our third shop as we speak,” said Brooklyn.
CSN Walkerton was initially seeking a something that would counteract any instances of human error in material tracking and ordering. “Challenges included a technician simply forgetting to write down a product they grabbed, or writing down an incorrect quantity for the amount of one item used. Intelligible writing also caused us to be charged and re-order products that weren’t necessarily the ones we used,” said Brooklyn. “We would definitely recommend 3M™ RepairStack™. It has greatly increased our business’ efficiencies through the ease of signing out products, inventory reporting and claim-specific invoicing.”
For more information on 3M™RepairStack™Performance Solutions, visit 3M.ca/RepairStack or contact your local 3M sales representative today.